What are Encoder Wheels?
An encoder wheel, also known as an encoder disc or a rotary encoder, is a type of electromechanical device used to convert rotational motion or position into an electrical signal. It’s commonly used in various applications to determine the position, speed, direction, and even acceleration of a rotating object.
The basic principle of an encoder involves a disc with alternating transparent and opaque sections (or sometimes slots and gaps) that is attached to a rotating shaft. As the shaft rotates, the light from a light source (such as an LED) passes through the transparent sections and is detected by a sensor on the other side of the disc. The sensor can be an optical sensor, magnetic sensor, or another type of technology that can detect changes in the pattern of the disc.

(https://fotofab.com/products/encoders/)
The sensor generates electrical signals based on the changes in light or magnetic field, and these signals are then processed by electronic circuits to determine the position and movement of the encoder wheel. They can be either incremental or absolute:
An incremental encoder generates a series of pulses as the disc rotates. These pulses indicate both the direction and the number of steps it has moved. By counting these pulses, you can determine the relative position and movement of the encoder.
Absolute encoders provide a unique digital code for each position of the disc. This means that even if the power is lost, it retains its position information. Absolute encoders are commonly used in robotic arms.
APPLICATIONS & EXAMPLES OF ENCODER WHEELS
Encoder wheels, whether they are incremental or absolute, find applications in various industries and technologies where accurate measurement of rotation, position, speed, and direction is crucial. Here are some examples of their applications:
- They are used to monitor the speed and position of conveyor belts in manufacturing and distribution centers.
- They help robots accurately control joint movements and track their positions for tasks like pick-and-place operations, welding, and assembly.
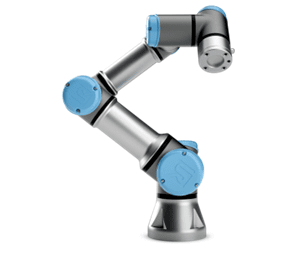
Figure 2. Universal Robot Cobot Arm uses magnetic encoders in each joint
(https://sp-automation.co.uk/sp-elements/universal-robots/ur3e/)
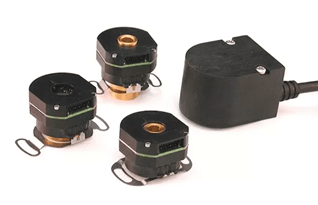
(https://www.quantumdev.com/optical-encoder-applications/cnc-machining/)
- They are used to provide feedback for precise control of the movement of cutting tools and workpieces in computer numerical control (CNC) machining.
- In servo motors they provide feedback to control the motor’s position, speed, and torque, allowing for precise motion control.
- They are used in ABS systems to measure wheel rotation and provide information for traction control and braking.
- They help determine the position and movement of the steering wheel for power steering and advanced driver assistance systems (ADAS).
- Encoder discs are used in aircraft control surfaces like ailerons, elevators, and rudders to ensure accurate control and stability.
- They assist in pointing and positioning satellite antennas for communication and data transmission.
- Optical encoders in computer mice track the movement of the mouse on a surface and convert it into cursor movement on a screen.
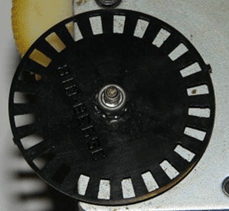
Figure 4. Encoder wheel used in mouse
(https://electronics.stackexchange.com/questions/15481/how-does-a-ball-mouse-know-the-direction)
- Encoders in audio equipment and home appliances control volume settings.
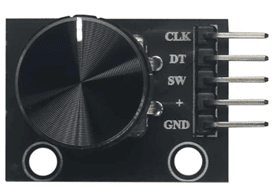
Figure 5. Encoder disc mounted on a circuit board.
(https://www.parallax.com/product/ky-040-rotary-encoder-module-15×16-5-mm-with-knob/)
- Encoder discs monitor the orientation and rotation of wind turbine blades to optimize their angle for maximum energy generation.
- They are used in solar panel tracking systems to follow the movement of the sun for optimal energy capture.
- They contribute to the precise movement of components in medical imaging equipment like CT scanners and MRI machines.
- They assist in the precise control of robotic surgical instruments.
- They ensure accurate paper movement and ink placement in high-speed printing presses.
- They help control the movement of packaging materials and products in packaging lines.
These are just a few examples of the many applications of encoder wheels in various industries. Essentially, any situation where accurate measurement of rotational movement, position, or speed is important can benefit from the use of encoder technology.
Using encoder wheels offers several advantages in a variety of applications due to their ability to provide accurate position, speed, and direction information. Some key advantages include:
- They provide high precision and accuracy in measuring rotation, position, and movement.
- They offer real-time feedback on the movement and position of rotating elements.
- They are versatile and can be used in a wide range of industries and applications, from industrial automation to consumer electronics.
- Optical encoders operate without physical contact between the disc and the sensor. This reduces wear and tear, increasing the longevity of the system.
- They can detect both the direction of rotation and the number of rotations, which is valuable in applications requiring accurate bidirectional movement tracking, like conveyor systems.
- Absolute encoders provide immediate information about the exact position, even after power loss. This is crucial in scenarios where maintaining position data is vital, such as power-sensitive systems or safety-critical applications.
- In applications like automotive anti-lock braking systems and industrial machinery, they contribute to enhanced safety by providing accurate data for control algorithms that prevent accidents or hazardous situations.
- They enable closed-loop control systems, where the actual position or movement is constantly compared to the desired position, allowing for adaptive adjustments based on changing conditions.
- The accurate feedback provided by them helps identify issues early on, allowing for proactive maintenance and reducing downtime due to unexpected failures.
- Encoder systems can often be customized to fit specific requirements, including the number of pulses per revolution, resolution, and communication protocols.
Overall, encoder wheels play a vital role in improving precision, efficiency, and control across a wide range of industries, making them an essential component in modern machinery and technology.
DISADVANTAGES OF ENCODER WHEELS
While they offer numerous advantages, there are also some disadvantages and limitations associated with their use. Here are a few disadvantages to consider:
- Encoder systems can be complex to design, install, and maintain. They can be relatively expensive, especially those designed for applications that require high precision and accuracy.
- Optical encoders can be sensitive to environmental conditions such as dust, dirt, moisture, and temperature fluctuations. These factors can affect their accuracy and reliability.
- In applications with physical contact between the encoder disc and the sensor, mechanical wear can occur over time, leading to reduced accuracy and the need for regular maintenance or replacement.
- The resolution of an encoder system determines its ability to measure fine movements.
- In environments with high levels of electromagnetic interference, such as industrial settings with heavy machinery, they can be susceptible to signal interference that affects their accuracy.
- In the case of single-turn absolute encoders, the absolute position measurement is limited to one full revolution. For applications requiring multiple revolutions, multi-turn absolute they are necessary, but these can be more complex and costly.
- Setting up and calibrating encoder systems properly can be intricate and time-consuming. It requires careful alignment and adjustment to ensure accurate readings.
- Over long cable lengths, especially in noisy environments, the encoder signals can degrade, leading to inaccuracies in the readings received by the control system.
- Like any electronic component, they can fail due to various factors such as electrical issues, mechanical wear, or manufacturing defects.
- In safety-critical applications, relying solely on a single encoder for position feedback can be risky.
- Integrating encoders into existing systems might require modifications and adaptations to the control system’s software and hardware.
- In systems with complex movements or interactions, interpreting the encoder data accurately can be challenging, particularly if the control system isn’t well-designed.
Despite these disadvantages, encoder wheels remain essential components in many industries due to their ability to provide accurate position and motion data. Careful consideration of the application’s requirements and potential challenges can help mitigate these disadvantages and ensure successful implementation.
MANUFACTURING OF ENCODER WHEELS
Manufacturing them involves several steps and can vary depending on the type of encoder and the technology used. Here’s a general overview of the manufacturing process:
Engineers design the encoder wheel based on the specific requirements of the application, including the number of segments, resolution, and other parameters. Prototyping might involve creating a sample to test its functionality and performance.
Encoder discs can be fabricated using laser cut technology, which allows for faster prototyping and testing. We specialize in laser cutting with as low as 50um sized apertures. We can also fabricate them using photochemical etching which allows for a high count of apertures.
The choice of materials depends on factors like durability, transparency (for optical encoders), and resistance to environmental conditions. Common materials include plastic, metal, or glass. The base material is machined or cut to the desired shape and dimensions using methods such as laser cutting, CNC milling, or stamping. This process creates the pattern of alternating transparent and opaque sections on the encoder disc.
In optical encoders, transparent sections might be coated with a reflective material to enhance the contrast and accuracy of the signal. For high-precision encoders, markings or etchings might be added to the disc to assist with alignment during assembly. If the encoder is an optical type, a light source (LED) and sensor (photodetector) are integrated into the housing, facing the disc. For magnetic encoders, magnets or magnetic sensors are integrated.
The encoder wheel is assembled into the housing, which protects it from environmental factors and ensures proper alignment with the sensor. Additional components such as bearings might be added to ensure smooth rotation. Each disc undergoes testing and calibration to ensure that it produces accurate signals and meets the specified resolution.
It’s important to note that the manufacturing process can differ significantly based on the technology used (optical, magnetic, capacitive, etc.) and the specific requirements of the encoder. Advanced manufacturing techniques like microfabrication and precision machining are often employed for high-performance encoders with demanding specifications.
FUTURE OF ENCODER WHEELS
The future of encoder wheels is likely to be influenced by several technological trends and advancements in various industries. We believe that the following improvements will follow the development of encoder wheels:
- There will likely be a push toward smaller and more compact solutions. Miniaturized encoders would find applications in devices where space is limited, such as wearable technology, medical implants, and miniature robotics.
- They are likely to become more integrated with the Internet of Things (IoT) and Industry 4.0 initiatives. This could involve adding communication capabilities to encoders to enable real-time data sharing, remote monitoring, and predictive maintenance.
- The use of advanced materials with specific properties, such as enhanced durability, resistance to harsh environments, or improved signal transmission, could lead to more robust and versatile designs.
- Optical encoders could see improvements in terms of higher resolution, better signal processing, and increased resistance to environmental factors like dust and moisture.
- They could adopt wireless communication protocols to eliminate the need for physical wiring, simplifying installation and reducing potential points of failure.
- Future encoder discs might be designed to withstand extreme conditions, including high temperatures, corrosive environments, and heavy vibrations.
- As energy efficiency becomes more critical, encoder technologies could focus on reducing power consumption while maintaining high accuracy.
- The data collected from encoder systems could be processed using advanced analytics and machine learning techniques to extract insights, optimize processes, and enable predictive maintenance.
- Encoder technology could play a role in more intuitive human-machine interfaces, enabling precise and responsive control in virtual reality, augmented reality, and haptic feedback systems.
- In applications like autonomous vehicles and drones, encoder systems will play a crucial role in accurately tracking movements and positions.
The future of encoder wheels is promising, shaped by ongoing technological trends. Miniaturization could lead to their integration in wearables and micro-robotics. Integration with IoT and Industry 4.0 could enable real-time data sharing. Advances in materials may enhance durability and signal transmission. Optics could see improvements in resolution and performance. As renewable energy and space exploration gain prominence, they may find new applications in uncharted territories.
In conclusion, encoder wheels are the uncelebrated heroes behind precision and control in diverse industries. They translate mechanical motion into actionable data, empowering automation, safety, and innovation. Despite challenges, their advantages far outweigh their disadvantages. As technology advances, encoder wheels will continue to evolve, propelling industries toward greater efficiency, accuracy, and progress.
Stencils Unlimited manufactures encoder wheels. If you would like to receive a custom quote, please email support@stencilsunlimited.com and our team will glad to help you.