Common Soldering Problems in the Printed Circuit Board Industry
There are several types of printed circuit board soldering problems that can occur during the manufacturing or repair process. Here are some of the most common ones:
SOLDER BRIDGE
A solder bridge occurs when excess solder connects two or more adjacent metal leads or pads on a printed circuit board, causing a short circuit. This problem can occur during the soldering process when too much solder is applied. It can also be caused by improper soldering techniques, such as using too much heat or pressure.
Solder bridges can be prevented by using the correct amount of solder and by ensuring that the soldering iron tip is clean and free of excess solder. Additionally, it is important to use the correct soldering techniques, such as holding the soldering iron at the correct angle and heating only one metal lead or pad at a time.
If a solder bridge has already occurred, it can be fixed by removing the excess solder using a solder wick or a desoldering pump. The excess solder can also be removed using a fine-tipped soldering iron while applying a small amount of flux to the area. It is important to avoid overheating the area and to remove the solder bridge carefully to avoid damaging the metal leads or pads.
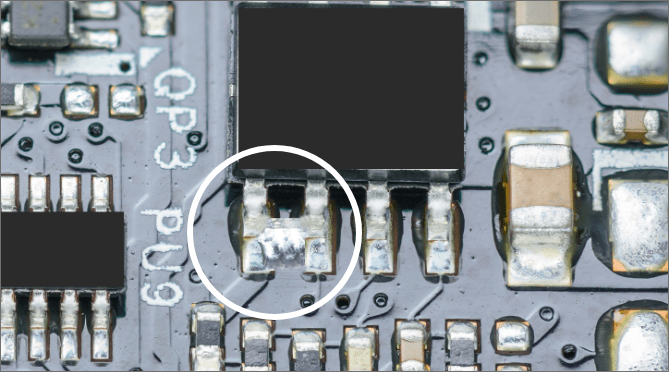
COLD JOINTS
A cold joint occurs when the solder does not fully melt or flow onto the metal leads or pads on the printed circuit board leaving a rough and grainy surface. Cold joints can result in poor electrical conductivity, intermittent connections, and mechanical weakness, which can lead to malfunctioning of the circuit.
Cold joints can be caused by a variety of factors, such as inadequate heat or improper soldering techniques. It can also happen when the soldering iron is not hot enough or when it is removed too quickly from the joint, not allowing enough time for the solder to properly flow and adhere to the metal leads.
To avoid cold joints, it is important to use the correct soldering tools and techniques. This includes using the right temperature on the soldering iron, using the correct type and amount of flux, and ensuring that the metal leads or pads are clean and free of oxidation before soldering. It is also important to hold the soldering iron on the joint for the appropriate amount of time to ensure that the solder fully melts and flows onto the metal leads.
To fix a cold joint, the first step is to reheat the joint with a soldering iron or hot air gun to melt the existing solder. Apply a small amount of fresh solder and ensure it flows smoothly into the joint, filling any gaps or voids. It may also be necessary to clean the joint with a solder wick or flux remover to remove any contaminants that may have prevented proper bonding.
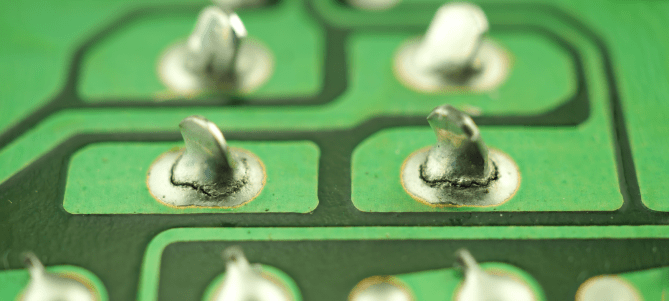
SOLDER SPLATTER
Solder splatter occurs when droplets of molten solder are splashed or splattered onto the surrounding components or areas of the printed circuit board. Solder splatter can cause short circuits, damage the components, and create poor-quality solder joints.
Solder splatter can be caused by several factors, including using too much solder, overheating the solder, and improper use of the soldering iron. Using too much solder can cause the molten solder to splash or spatter onto other areas of the printed circuit board. Overheating the solder can cause it to boil, which can result in splattering. Improper use of the soldering iron, such as holding it at the wrong angle or applying too much pressure, can also cause solder splatter.
To prevent solder splatter, it is important to use the correct amount of solder and to avoid overheating the solder. It is also important to hold the soldering iron at the correct angle and to apply gentle pressure to the metal leads or pads. Additionally, using a soldering iron with a smaller tip can help prevent splatter by focusing the heat on a smaller area.
If solder splatter does occur, it can be cleaned using a flux remover or an alcohol-based cleaner. It is important to be gentle when cleaning the area to avoid damaging the components or the printed circuit board.
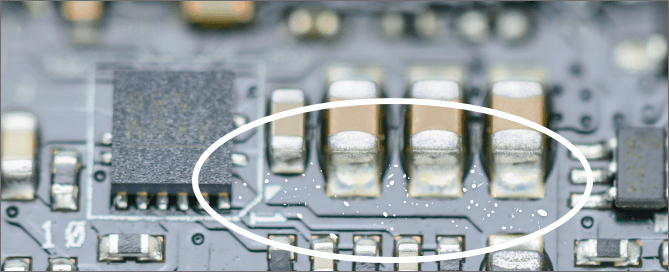
TOMBSTONING
Tombstoning occurs when a SMT component lifts from one end and stands vertically on the opposite end, resembling a tombstone. This is usually caused by uneven heating or cooling of the component during the soldering process, resulting in a temperature gradient across the component.
To prevent tombstoning solder, it is important to make sure that the components are placed correctly, and that the right amount of solder paste is applied to each pad. It is also important to make sure that the temperature profile is balanced, and that the heating and cooling rates are under control to prevent uneven heat distribution of the components. Additionally, using a reflow oven with proper airflow can help prevent tombstoning solder during SMT soldering.
To fix tombstoning, ensure that the component is held firmly in place during the soldering process, and that there is even heating and cooling across the component. Use a hot air gun or preheating station to ensure even temperature distribution or reflow the solder using a reflow oven.
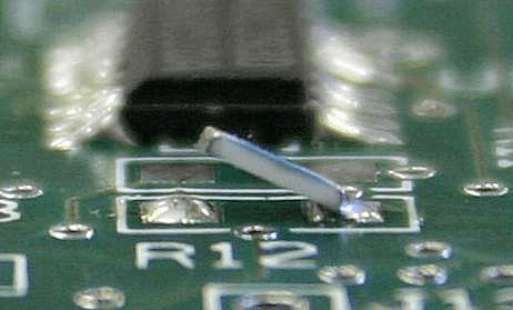
INSUFFICIENT SOLDER
Insufficient solder occurs when there is not enough solder to make a proper connection between the component and the printed circuit board, resulting in a weak or intermittent connection. This can be caused by a lack of flux or improper soldering technique.
To avoid this problem, it is important to use the proper amount of fresh solder and to heat the metal surfaces to the correct temperature before applying the solder. Additionally, using a soldering iron with the proper wattage and tip size can help ensure that the solder melts and flows correctly.
To fix insufficient solder, apply additional solder as necessary to create a strong and reliable connection, as well as adding a small amount of flux to the joint to ensure proper bonding. Make sure that the solder flows smoothly into the joint and fills any gaps or voids.
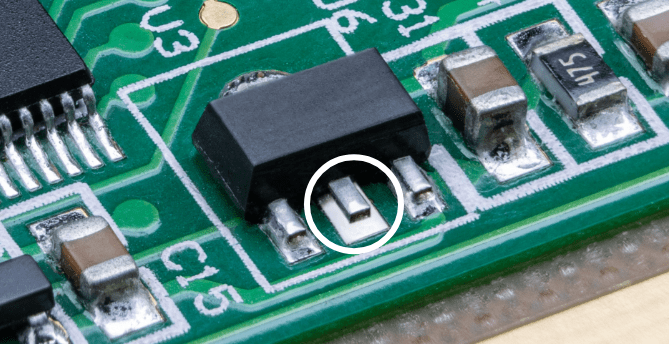
PREVENTING SOLDERING PROBLEMS
Soldering problems can be frustrating, but they can also be easily fixed with proper technique and attention to detail. By understanding the common causes of soldering problems and their fixes, you can ensure a reliable and high-quality connection between components and printed circuit boards. The following are recommendations to minimize the number of soldering problems.
Properly Prepare the Printed Circuit Boards and Components
Properly preparing the PCB and components before soldering can also help prevent issues. This includes cleaning the PCB with a solvent or alcohol to remove any contaminants and ensuring that the components are properly aligned and secured. It also involves ensuring that the components are not damaged or corroded, and that the PCB is not warped or damaged.
Use Proper Soldering Techniques
Using proper soldering techniques is essential to prevent soldering issues. This includes using the appropriate temperature and soldering iron tip size for the job, using sufficient flux, and applying the right amount of solder. It also involves ensuring that the components are held in place during the soldering process, and that there is even heating and cooling across the component.
Use Quality Solder and Flux
Using high-quality solder and flux can help prevent soldering issues. Low-quality solder or flux can result in poor bonding, inconsistent flow, and other issues. Choose a reputable brand and check the manufacturer’s specifications to ensure that the solder and flux are suitable for your specific application.
USE THE PROPER SMT STENCIL DESIGN AND OPTIMIZATION
Some soldering problems are introduced during the printing process. These problems can be prevented with the proper SMT stencil design. Our CAD engineers can help you design your SMT stencils to make sure that the correct amount of solder paste is used to avoid bridging, insufficient solder, blobs, and tombstoning issues. You can quote and order all our SMT stencils online.